New York Burn Injury Lawyers Discuss Common Causes of Industrial Fires
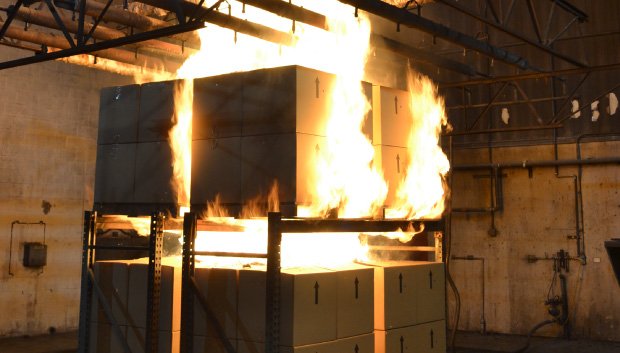
Every year, American fire departments respond to an average of 37,000 industrial fires that cause 18 civilian deaths, 279 civilian injuries, and roughly $1 billion in property damage explains one of the New York burn injury lawyers at the F&A accident law firm in Manhattan. Since government efforts to better regulate workplace safety aren’t always successful, individual employers must decide to fully protect their workers. Recognizing the most frequent causes of workplace fires can benefit everyone.
The Most Common Causes of Industrial Fires
- The improper presence or storage of liquids and gases
- Combustible dust
- Ongoing “hot work” that includes torch cutting and welding – as well as soldering, heating, burning, and brazing;
- Electrical wiring and related hazards
- The improper use and maintenance of equipment
Each of these five topics is addressed further below, along with general safety guidelines.
Safer Handling of Flammable Workplace Liquids and Gases
All workplace supervisors must familiarize themselves with the Safety Data Sheets (SDS) for all hazardous liquids or substances that are used on the job. Ongoing employee training is also required to make sure all ignition sources used with flammable substances are handled properly.
Furthermore, all personnel authorized to work with flammable substances must be provided with high-quality protective gear.
Proper Handling of Combustible Dust
Far too often, employers fail to arrange for the proper removal of all combustible dust that’s produced during woodworking, metalworking, the making of pharmaceuticals, foods, chemicals, dyes, and other goods. Once a large, combustible dust cloud forms, it can quickly cause explosions, serious injuries or even deaths.
Employees hired to handle combustible dust must be properly trained to avoid different types of injuries. Back in September of 2015, a worker in Winterville, Georgia was severely burned while operating a dust collection machine. Fortunately, he managed to survive. An excellent 2014 New York Times article documents how common these types of accidents have become. The most critical safety precaution involves routinely collecting combustible dust before properly disposing of it.
Only Fully Trained Personnel Should Be Allowed to Handle “Hot Work” Tasks
Employers should only allow their most experienced welders to handle highly complex and dangerous assignments. Work areas must also be properly insulated since molten materials and sparks can fly off quickly while “hot work” is being done, setting fire to any flammable goods or surfaces nearby.
It’s often wise to require at least one higher-ranked employee to supervise all hot work activities. Should an accident occur, two well-trained workers will be present and at least one should remain fully capable of stopping the spread of any fire that might start.
Poorly Maintained or Improperly Used Equipment/Nearby Furnaces
Every industrial workplace requires fully updated equipment that’s routinely checked and repaired to minimize fires or other dangerous events. Also, all furnaces must be properly cleaned and maintained. Finally, workers must be reminded that many pieces of mechanical equipment can overheat due to internal friction, increasing the chances of a fire breakin out.
Only Highly Trained Personnel Should Be Allowed to Handle Electrical Tasks
The proper voltage level must be marked on all equipment and every worker must wear appropriate safety gear. Daily inspections must be conducted to prevent overloaded circuits and outlets. In addition, extension cords must be used sparingly — and all personnel must be reminded of the dangers of static discharges.
Once sparks start flying during electrical work, they can quickly cause fires, especially when there’s too much combustible dust in the area.
Routine Hazard Analyses and Safety Practice Reminders Are Critical
Employers must conduct weekly (if not daily) assessments of all workplace fire hazards to fully protect all workers and business investments. Supervisory personnel must also regularly:
- Post signs and verbally remind all workers to never smoke in forbidden areas – always imposing stiff fines or even firing those who disobey these safety rules;
- Require all employees to wear protective gear when handling hazardous tasks;
- Have a building evacuation plan in place and conduct fire drills at least two or three times a year – and remind employees of the proper exits during staff meetings in between drills;
- Take extra safety precautions whenever installing and starting to use new equipment;
- Fire safety training must be presented as part of all new-employee orientation meetings and presented to the entire workforce at least once or twice a year;
- Require one or more employees to turn in hazard evaluation sheets before leaving work at least once a week – and make sure their supervisors immediately address all problems;
- All workplace fire extinguishers, sprinklers, and other safety equipment must be tested at least once every six months. It’s also wise to ask a local fire marshal to visit and inspect your workplace once or twice a year.